油圧システムをアクティブに保ち、効率的に動作させるためには、メンテナンス計画が不可欠です。メンテナンス計画は、将来の修理費用を削減し、予定外のダウンタイムを最小にし、全体的なオペレーションの収益性をサポートします。予防的な保守手順を積極的に行うことで、油圧システムと部品をより良い状態に長く保つことができます。
予防保全(PM)プログラムには、大きく分けて2つの部分があります。継続的なプロセスとコミットメントとして、定期的なメンテナンスだけでなく、運転前後の点検の計画も含まれます。
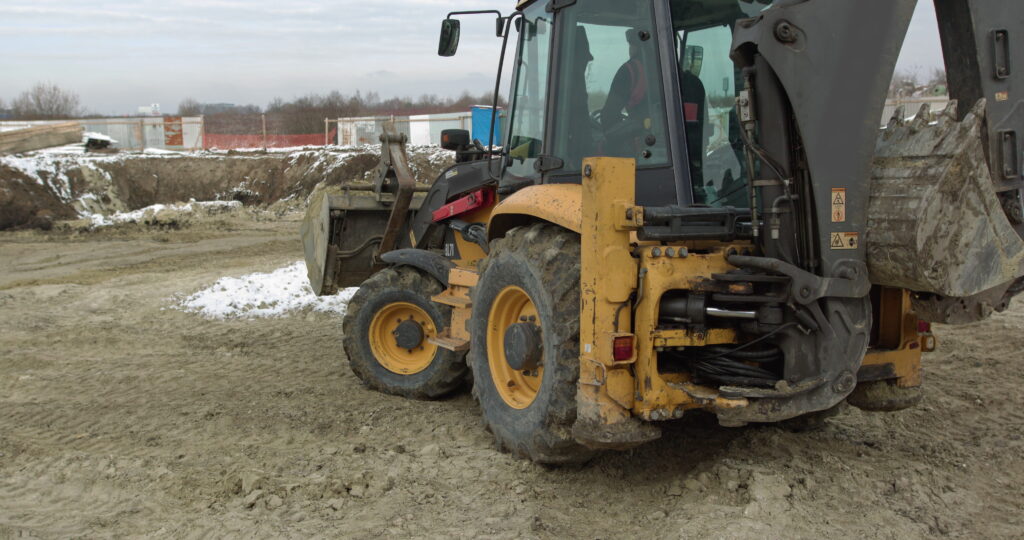
問題の予防と是正。
油圧システムを維持し、トラブルを防ぐには、機械とどの部品が最も摩耗しているかを知る必要があります。例えば、マニュアルやOEMの推奨からメンテナンス情報を確認することは、機器の適切な長期的ケアにつながります。
を特定した上で 潜在的問題また、メンテナンスの際には、直ちに是正処置を行うようにしてください。また、不具合の報告を怠ると、故障の発生や操業の遅れにつながります。特にホースと油圧システムについては、定期的な予防保全プログラムを策定することが重要です。
ここでは、メンテナンス計画を実行するためのヒントを紹介します。
STEP 1: メンテナンス計画を明確にする:
メンテナンス計画を作成する最初のステップは、各点検でルーチンがカバーするものを正確に定義することです。通常、メンテナンス計画では次の3つの点をカバーします。定期的なメンテナンス、定期的な点検、先取りした部品交換など。
STEP 2: 検査の日程を決める。
次のステップは、定期メンテナンスと予防メンテナンスのタスクをスケジュール化することです。ベストプラクティスの一例として、メンテナンススケジュールを分けておくことが挙げられます。例えば、定期点検用、一般点検用、部品交換用と分けておくと、整理整頓ができます。さらに、機械の予防保守や点検活動については、常にメーカーの推奨事項を確認し、定期点検時にすべての項目が適切に見直されるようにします。
STEP3:メンテナンスの活動を記録する。
すべてのメンテナンス活動は、一カ所に記録されるべきです。もし、複数の重機を所有しているのであれば、それぞれ別の記録を持つのがベストです。つまり、サービスや点検の活動を記録することで、たとえ別々のスケジュールであっても、全員が予防メンテナンスの責任を負うことができるのです。また、予防保全や定期点検を積極的に行うことを優先させる習慣を身につけることにもつながります。
STEP4:担当者を指定する。
予防保全計画を完成させるには、その計画に関連するすべての活動の責任者を任命する必要があります。例えば、中小企業では、オーナー経営者や社長が保守・点検の管理を行うのが一般的です。一方、大企業では、メンテナンス活動を監督する重機技術者の責任者を雇うのが一般的です。しかし、会社の規模によっては、このようなことはできません。
すべての選択肢を評価する
油圧システムコンポーネントの寿命を延ばすことは、予防保全プログラムの中核的な目標です。これらの問題を常に把握しておくことは、投資した時間と費用に対して多大な見返りをもたらします。さらに、次のことを検討する必要があります。 蛍光式リークディテクション.システムの初期段階で、オイルと共に安全に循環する蛍光性の漏れ検知用染料を組み込むことができます。これは、汚染物質が形成され、より大きなシステムの問題につながる前に、リークをキャッチするためのものです。リークディテクターと定期的なメンテナンス計画を組み合わせることで、劣化した故障を初期段階で検出し、一過性の故障を遅らせたり、致命的な故障を回避したりすることができます。
蛍光灯による漏れ検査が、お客様の運用・保守計画にどのように役立つかをご覧ください。